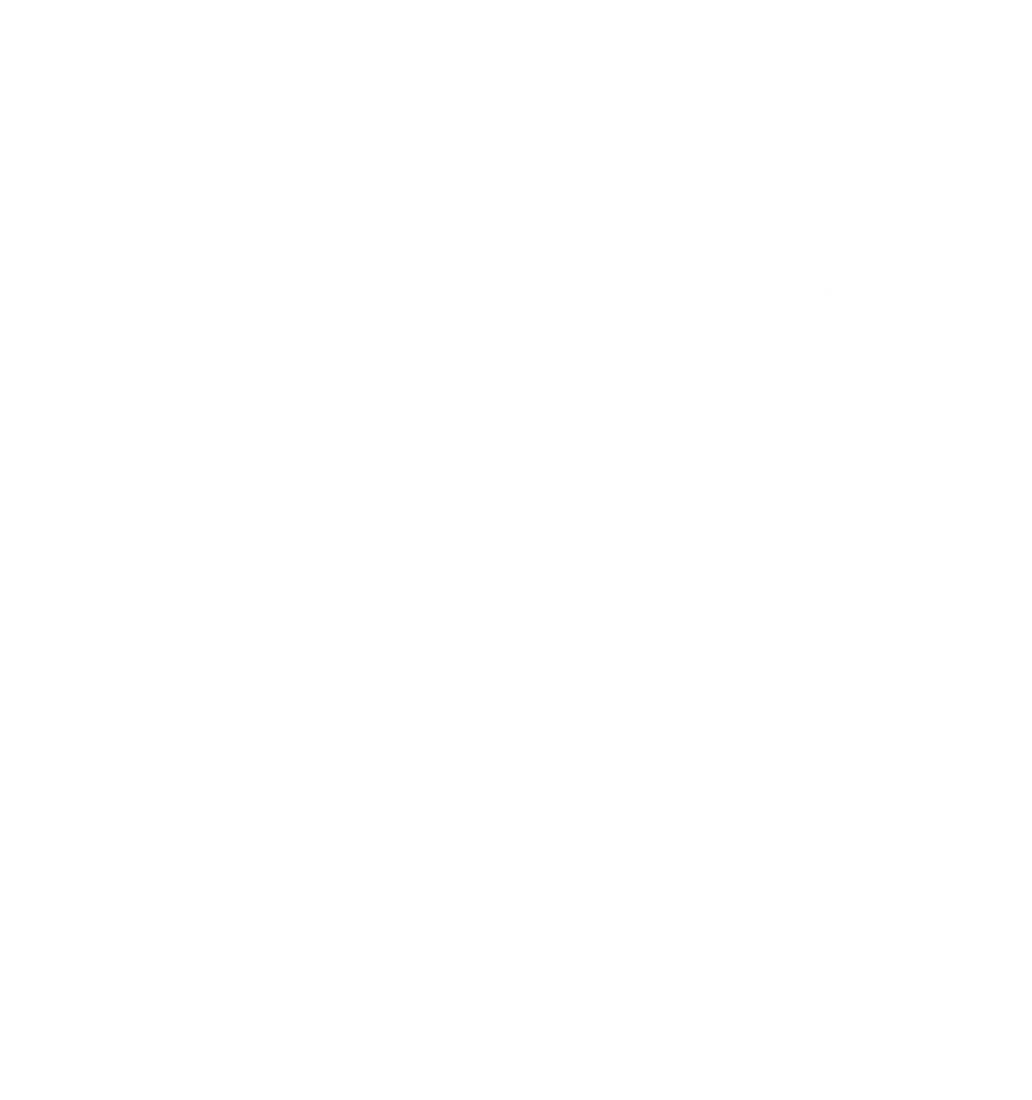
What is Riso?
Riso Kagaku is a Japanese corporation founded in 1946 by Noboru Hayama in Tokyo, Japan.
They are the inventor, manufacturer, and distributor of the Riso printer-duplicator, a.k.a. Risograph.
In Japanese, riso translates to “ideal” and kagaku to “science.”
The Risograph machines were developed in 1986, it merges the charm of traditional handcrafted prints with the speed, cost-effectiveness, and efficiency of modern printing technology.
Despite its appearance resembling a copy machine, it's important to note that the Risograph isn't a copier but rather a duplicator.
The Risograph generates a stencil, which is applied to a rapidly spinning ink-filled drum. This high-speed rotation propels the ink through the stencil onto the paper, resulting in absorption and giving rise to a distinctive visual appeal and texture.
Nowadays the Riso inks are made from rice bran oil, and take longer to dry than conventional printing techniques.
Our Riso MZ 1070E prints two colours in one pass on A3 paper. It uses ink drums as spot colours to create 1 or 2 colour(s) duplications at high speed. More than 2 colours will require more than one pass through the machine.
Keep in mind that Riso ink is transparent, two different colours creates a third one.
Format and margin:
Max paper size: 297 x 420mm
Print files:
● Flattened PDF (no layers or transparencies)
● Set to Greyscale / B&W
● Resolution = 300 dpi
● Each colour layer must be a separate file
● Attach a colour preview for reference
Good to keep in mind:
● Minimum print run: 25 pieces.
● The Risograph is inherently imperfect and in our eyes, it’s part of its charm!
● Registration is fairly accurate with two colour design as the Riso prints two colours at the same time. Printing more than two colours will require more than one pass, and is best to assume that mis-registration will occur.
● Colour coverage can vary across large patches of ink. Flat colours are never perfectly homogenous if the inked area is too large.
● Please make sure you set large flat colour areas between 80% and 90% opacity and never at 100%.

● Paper can smudge on contact with rollers or other sheets (especially with higher ink densities).
● Roller marks can appear, especially when printing more than two layers or double sided. If you want to avoid them: Use less ink in the middle of the design. But these can easily be rubbed off with an eraser.
FYI: the rollers are 2cm.
Paper:
Riso printing requires printing on uncoated paper of minimum 60g and maximum 250g, short grain direction paper is recommended.
Paper in stock (varies):
Short grain
● 80g Fabriano Copy Bio
● 100g Arena Rough Natural
● 120g Arena Rough Natural
● 140g Arena Rough Natural
● 170g Arena Rough Natural
● 200g Arena Rough Natural
● 250g Arena Smooth Natural
● 270g Mohawk Eggshell
Long grain
● 90g Arena Rough Natural
● 100g Arena Rough Natural
● 120g Arena Rough Natural
We also have some coloured papers in stock, ask us!
We print on uncoated paper only.
You can also bring your own paper, but remember to bring a little more than necessary!
Grain direction:
It is very important when binding books to avoid the paper to “crack”, create a rough fold or even resulting in a book that stays a bit open when it’s supposed to be closed.
For bookbinding, you should always fold with the grain direction parallel to the fold and the spine of your binding to have a smooth opening.
Short grain or long grain direction paper matters only when you need to make a book or need to have a fold.
Confused? We can help you!
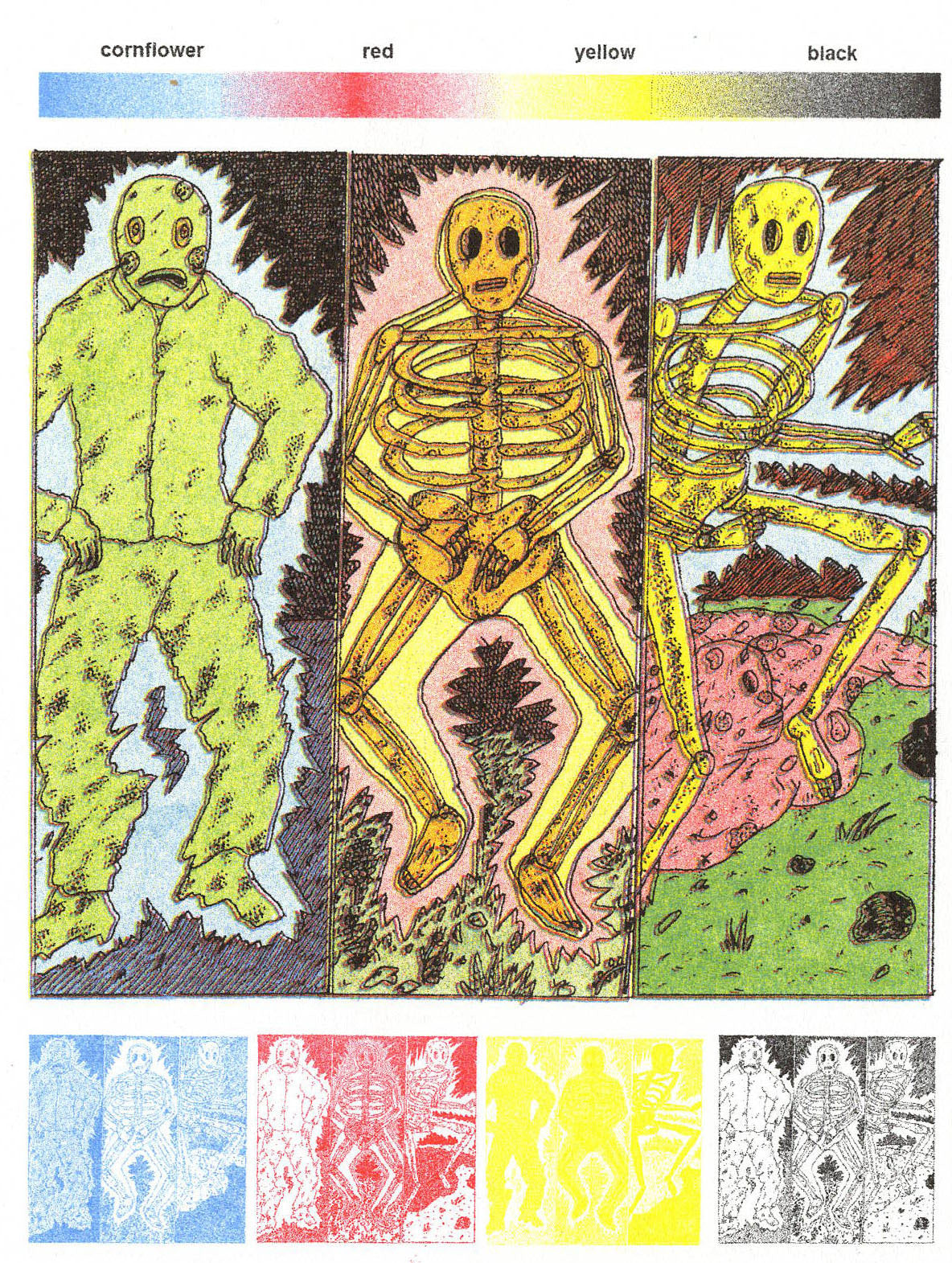
CMYK:
Perfect CMYK printing doesn’t exist with Riso, Magenta and Cyan are not available inks.
However, it is possible to use Red and Cornflower blue instead.
It is possible to translate a CMYK with 3 or 4 inks using different colour combinations.
The outcome will differ slightly from the original colours, but it has the potential to evolve into something quite intriguing!
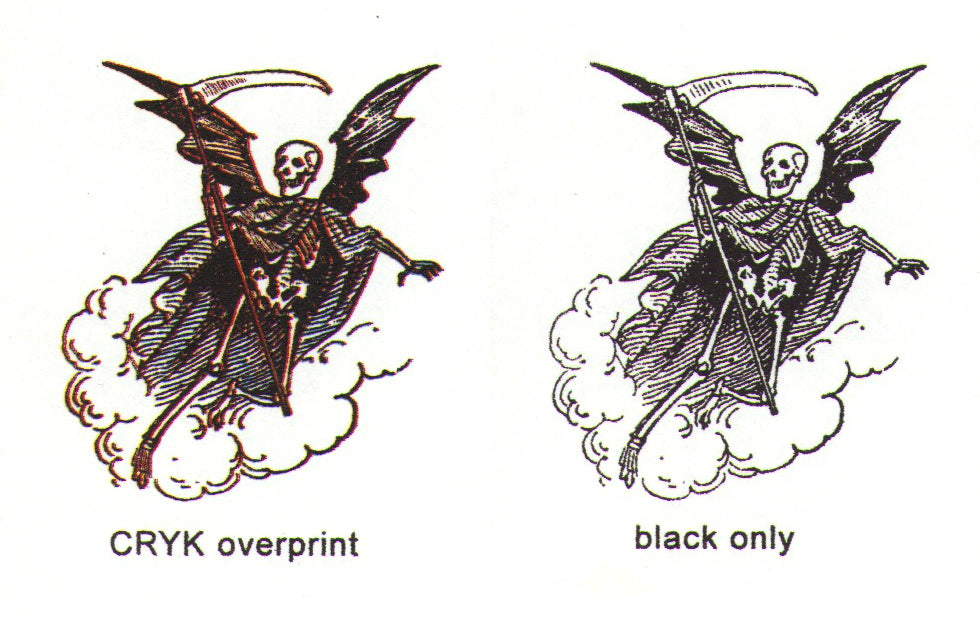
Overprint:
Due to the printing shifts in Riso, it is not recommended to overlay multiple colours for small texts or fine elements such as lines.
To avoid an overprint on text:
use a 100% black (0/0/0/100)
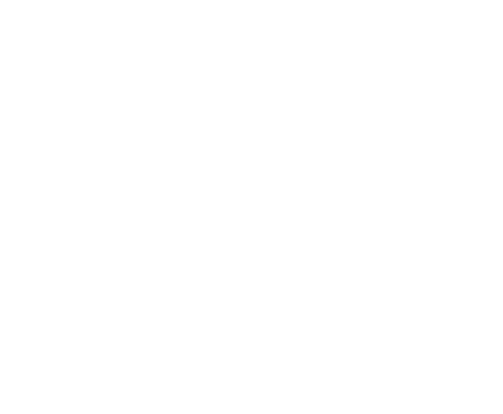
Typeface:
Text size should not go under 6 pt and avoid very thin typefaces.
Lines should not go under 0,25 pt.
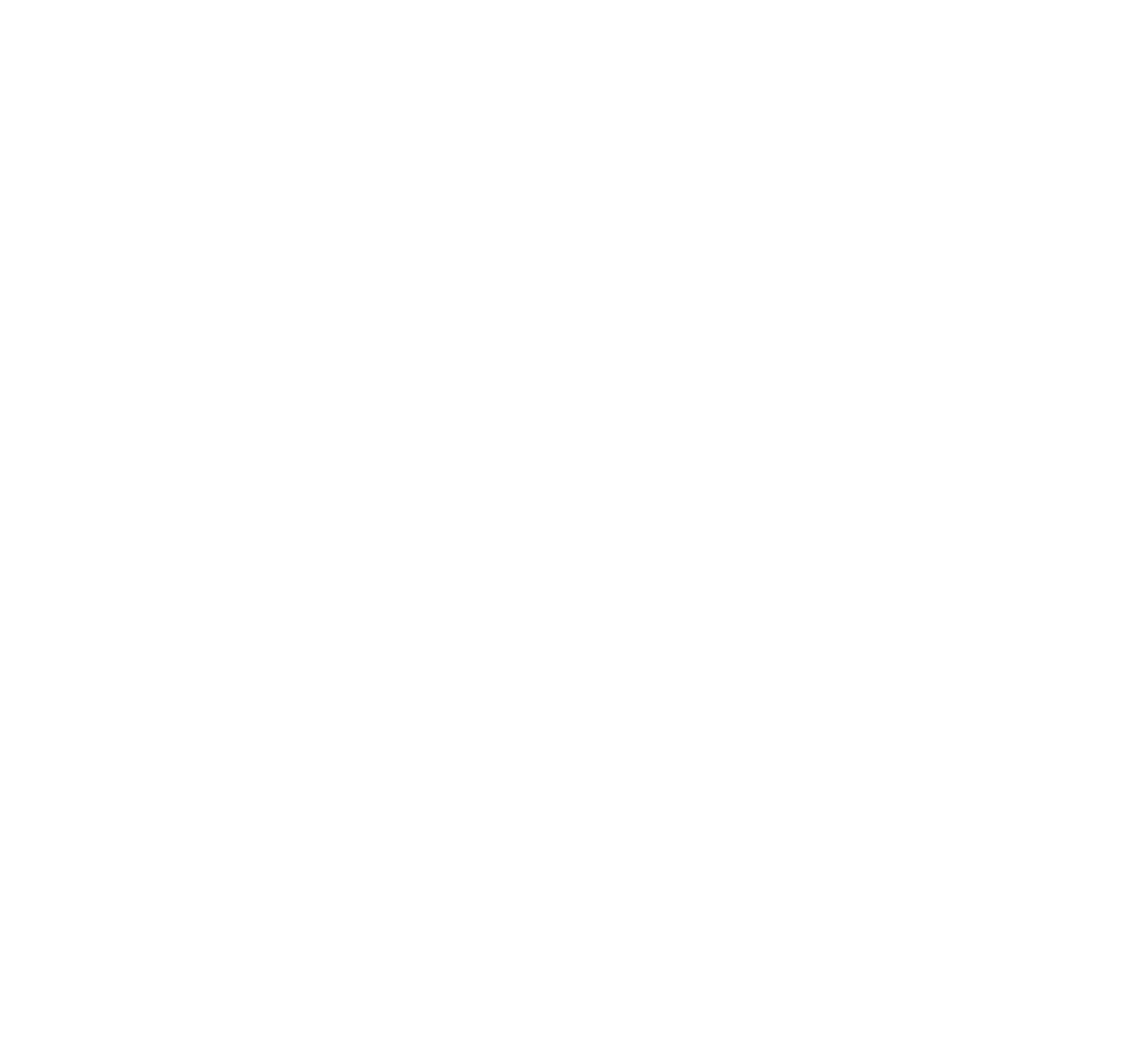
Binding:
We are able to do very basic binding in our studio:
● saddle staple
● saddle loop staple
● spiral binding
● perforation
Need another kind of binding or special service?
We also work with local binders.
Test print:
Running a test print or a proof is difficult because masters can’t be reused.
We can do a test print for a fee of €5 per colour / per A3
Deadline:
The production time varies depending on our calendar.
Prints with more than 2 layers will generally take longer as we need to allow a drying time in between the layers.
Need a quote?
riso@terrybleu.com
